Whatever happened to winter servicing?

Times are changing and, in today's world, the traditional winter service in our part of the northern hemisphere is becoming something of a rarity. Our climate is changing too, with variable mowing conditions throughout the year. Gone are the days of parking up the mower, stripping it down, checking it for wear and rebuilding it freshly painted with new parts and lubricants. It may have then been parked in the shed for two months until the grass started growing again.
Service on annual basis
Nowadays, mowers tend to be mowing for a large proportion of the year and it makes commercial and economic sense to service the machine on an annual basis. With finances in both the local authority sector and the golf sector under severe pressure, it makes perfect sense to ensure that service schedules are adhered to. So, if a machine is purchased during the height of the cutting season, it will require its annual service at the same time the following year, and this needs to be scheduled into the maintenance regime.
Change as required
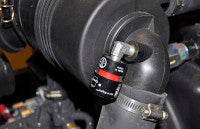
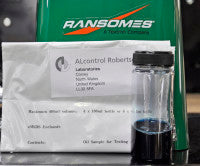
Making it easier
Ensuring that daily operator pre-start checks are carried out is often one of the most difficult disciplines to instill into an operator. The problem is that the majority of us drive modern day vehicles and, most mornings, we simply jump in, turn the key and drive to our destination. At the end of the working day, we do exactly the same, because motor manufacturers have designed out the requirement for daily checks.

As manufacturers, we are now producing machinery with less daily check points and, where possible, these are visual rather than mechanical, reducing debris ingress and contamination. Weekly and monthly check points have also been reduced to a minimum with the introduction of sealed units and bearings. Examples of this would include cutting units, steering axle assemblies and, on rotary decks, replacing drive belts and pulleys with hydraulically driven components.
And easier still!
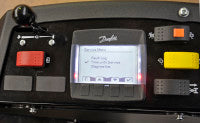
Braking systems have also improved dramatically. Many machines now use hydraulic wet disc brakes, instead of earlier drum or band brakes systems, which created huge servicing issues, costly repairs and maintenance as well as poor performance.
Engines and hydraulic systems have also benefitted from improved technology, with oil coolers and radiators being replaced with more efficient heat exchanger units. Improved technology has also been applied to the warning systems, which notify the operator of an issue.
Digital display screens offer more information, and horns and buzzers give the operator clear, audible warnings. Some systems even record the number of warnings given to the operator, so that accurate investigations can take place in the event of a major failure.
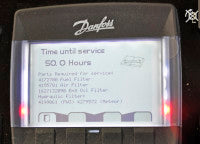
However, there's no getting away from it - all these items do require service and attention. So, getting the machine fully serviced by a main dealer or approved workshop, is an essential way to ensure that all the systems on the machinery are working correctly.
And what about fuel maintenance?
So far, we have looked at all the things manufacturers are doing to modern machinery to reduce maintenance and running costs. There are, however, changes to the engines we all fit, that will have an impact on everyone's routine maintenance as these changes are introduced.
From 2014 onwards, any machinery fitted with an engine over 50hp has to meet much tighter emission controls - in Europe this is known as Stage IIIB and, in the USA, as Tier 4. These new regulations affect all manufacturers and have been introduced to reduce emissions still further.
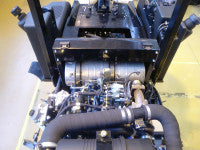
To further reduce NOx gasses and particulate matter, such as soot and harmful metals, a diesel oxidation catalyst (DOC) and a diesel particulate filter (DPF) are also incorporated in the system.
Of course, all these additional specialised emission critical items have to be serviced more conscientiously than standard engine components; otherwise the Stage IIIB/Tier 4 engine performance will be greatly reduced, as well as the engine life. This will mean that the EGR cooler and hose/piping system has to be inspected every 1,500 engine hours and, every 3,000 engine hours, the DPF has to be removed and professionally cleaned or replaced.
Although these High Pressure Common Rail diesel engines are capable of producing cleaner emissions, due to the type of fuel injection system they use, it does mean that the fuel which goes into the engine now has to be much, much cleaner.
The major engine manufactures recommend using Ultra Low Sulphur diesel with a sulphur content less than 15 parts per million and with less than 0.05% moisture content. The fuel filters they are now fitting are working down to 2 microns, that's 2 thousandths of a millimetre!
So, end users need to be more particular about the fuel they are buying and how they store and filter it. If not, fuel filters will need to be changed frequently as they will become blocked by even low levels of contamination.
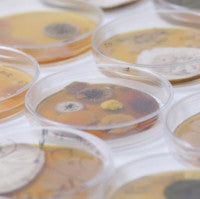
The issue which complicates this further is the introduction of biodiesel to the system. Biodiesel absorbs more moisture from the atmosphere, and this, together with the bio content, provides a breeding environment for bacteria, which produce moulds and a slime-like growth in the fuel. This blocks the filters and can stop the engine.
To prevent the likelihood of this occurring in storage tanks, fuel should be turned over regularly (at least 2 or 3 times a year), perhaps purchasing smaller quantities, more regularly. Storage tanks also need cleaning and regular fuel inspections to test for moisture content and contamination levels. It is better to improve the total management of the fuel system, than it is to buy expensive fuel filters and risk damaging very expensive engines!
As the bio content increases in our diesel, and the higher specification Common Rail engines become more widely distributed, then fuel systems will need increasing levels of maintenance. In future, end-users can protect themselves from potentially expensive repairs by managing and maintaining their fuel systems carefully.
The most important item in any maintenance regime
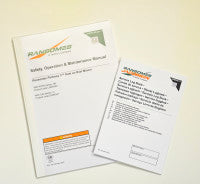
It's the most important part of the machine as it shows you how to use it, what the machine is capable of doing ... and when you should be maintaining it.
Conclusion
Like many things in life, the winter service has changed; or perhaps a better description is that it has morphed into a year-long regime of planned maintenance. We've made it easier and we'll make it easier still as equipment develops, but you can't beat doing the basics. Having good daily/weekly cleaning and checking practices will go a long way to ensuring a good performing and reliable machine.